Research project objectives/Hypothesis
The hypothesis of the research project assumes that it is possible to develop a robust three dimensional fully coupled, random cellular automata finite element (RCAFE) model for reliable full field simulations of microstructure evolution during a high temperature deformation under dynamic recrystallization (DRX) conditions.
Therefore, two main goals of the research are defined:
- development of the new class of full field models for dynamic recrystallization simulations, based on a full coupling between two computational techniques random cellular automata (RCA) and finite element (FE) methods,
- evaluate the robustness of the proposed new computational model of DRX under various model setups and process conditions.
Research methodology
The numerical part of the project requires skills in numerical modeling and model development as well as an access to the digital material representation and FE software. The Abaqus FE software is available in the AGH Cyfronet for the use in the current project on a daily basis. The PI and his team have developed a simplified inhouse 2D DRX RCA code that will be the basis for the present research. The crystal plasticity code used during the simulation is available through the cooperation with the UCL University in Belgium. Developed
models will be implemented using the object oriented C++, Phyton and Fortran programming languages. For the experimental part, the PI and his team have direct access to the rolling mill, optical and scanning electron microscopes, electron back scattered diffraction detectors, high temperature in-situ tensile stage. To reach project goals special clamps for high temperature in-situ SEM compression as well as small in-house in-situ heating stage will be used.
Research project impact
The dynamic recrystallization along with recovery are two groups of phenomena, which take place under hot deformation conditions and have crucial impact on a microstructure evolution. Thus, from experimental point of view, it is off importance to understand all physical mechanisms controlling mentioned phenomena in a wide range of metallic materials and processing conditions. Laboratory investigations can be additionally extended by series of numerical simulations that can provide insight into materials behavior that is difficult or sometimes even impossible to be evaluated experimentally.
The most standard DRX models are the phenomenological ones. Such models are based on a large number of assumptions and do not describe explicitly the physical mechanisms taking place during treatment. These approaches provide only an average information on the state of the material e.g. average grain sizes and local microstructure heterogeneities cannot be properly taken into account. Additionally, since the beginning of a new millennium these approaches have not always been providing satisfactory description of a material behavior. This is mainly related to the fast development of modern metallic materials like complex multi-phase materials.
That is the reason why it is so important to develop numerical models that can take into account the underlying microstructure morphology and its evolution in an explicit manner. Therefore, in the present research primary interest is put on development of a complete new class of DRX models based on the CA method. The solution is founded on a direct full coupling of a variation of the CA method called the random cellular automata method with the finite element method. The random CA method is responsible for modelling of microstructure evolution progress in an explicit manner while direct coupling with the FE naturally solves the problem of computational domain deformation issue. The concept of the concurrent RCAFE (random cellular automata finite element), in contrast to the classical CAFE method, lies in the assumption that the cellular automata cells directly correspond with finite element integration points. As a result, the microstructure evolution during a nucleation and subsequent growth is modelled by the RCA algorithm and the deformation of investigated computational domain is predicted by the finite element model. The developed model will introduce a new level of accuracy in prediction of phenomena occurring under dynamic recrystallization conditions, which is crucial for development of modern processing routes of new ,materials.
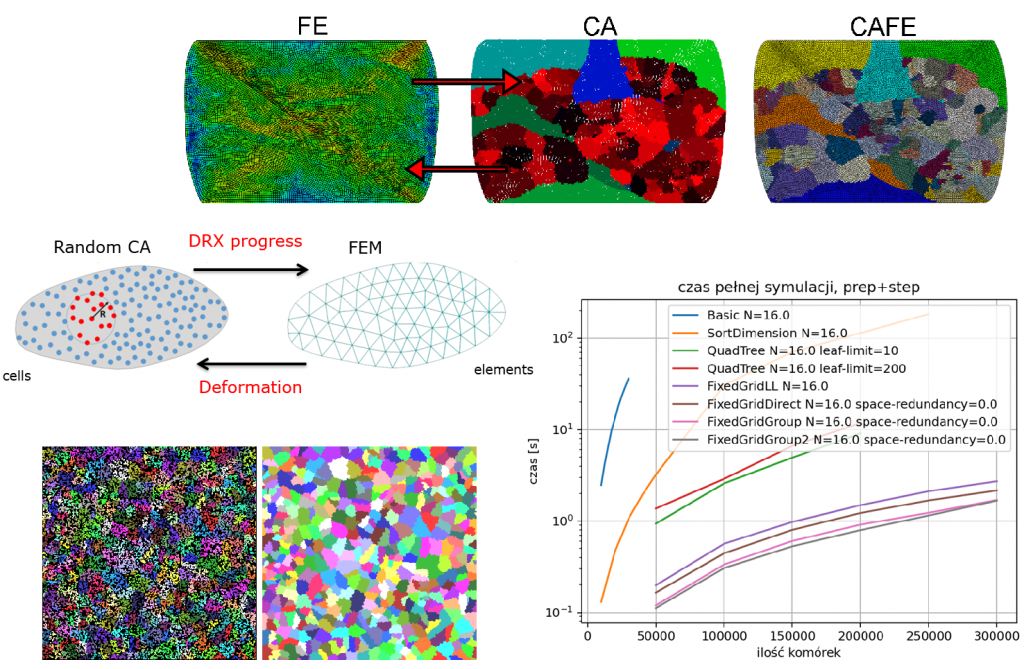